采用真空技术的精密自动化
Piab的真空驱动搬运系统和机器人工具在全球每一个工业领域中都得到了应用。我们量身定制的解决方案支持从原材料处理到单个物体的组装、分类和包装的应用,无论其尺寸、重量、形状或生产过程中的等级如何。
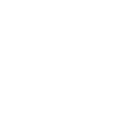
生产力
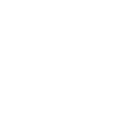
Piab的真空驱动解决方案显著减少了人工劳动,提高了生产力,保持了性能的一致性和质量标准的维持。
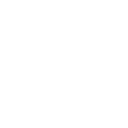
灵活性
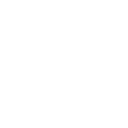
真空驱动系统减少了有害的工作任务,并使得安全搬运工业组件成为可能,这些组件从粉末和颗粒到大尺寸和重量的单个物体都有。
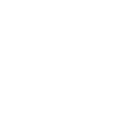
可持续性
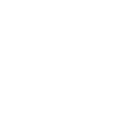
由于其技术和设计,Piab真空系统确保使用寿命长,维护少,能耗低,从而减少了对环境的影响。
您的企业属于哪个行业?
COAX® - 优异的真空发生器
基于我们享誉全球的COAX®喷射器的系统提供比传统真空系统多三倍的真空流量,从而提高循环速度并降低能耗。Piab发明了COAX®,因此我们的真空泵主要基于这种发生器技术。

真空自动化部门
Piab真空自动化部门是真空技术和机器人工具的全球领导者,可在各工业领域提高生产力,安全性和效率。通过标准化产品和定制解决方案的结合,我们能够以更小的能源消耗和材料浪费实现安全的工作环境。
探索
设计您自己的真空系统
OVM Pro 3D 可让您在实际实施前,在虚拟环境中设计、测试和完善您自己的真空系统。登录并使用 Piab 种类繁多的真空发生器、吸盘、抓手、接头和配件来创建独特的应用。
转至 OVM Pro 3D

最新消息
Product news
2025/6/17
BXP 系列推出全新尺寸:6 毫米和 8 毫米
我们广受赞誉的 BXP 吸盘专为搬运表面多孔/无孔的物料而设计,现在新增 6 毫米和 8 毫米两种尺寸,直径范围从 6 毫米扩展到 110 毫米。这一新增增强了我们模块化设计的多功能性。
DURAFLEX® 材料结合了橡胶的弹性和聚氨酯的耐磨性,可确保无痕提升,因此 BXP 系列在提升纸板等不平整和多孔物料方面表现出色。
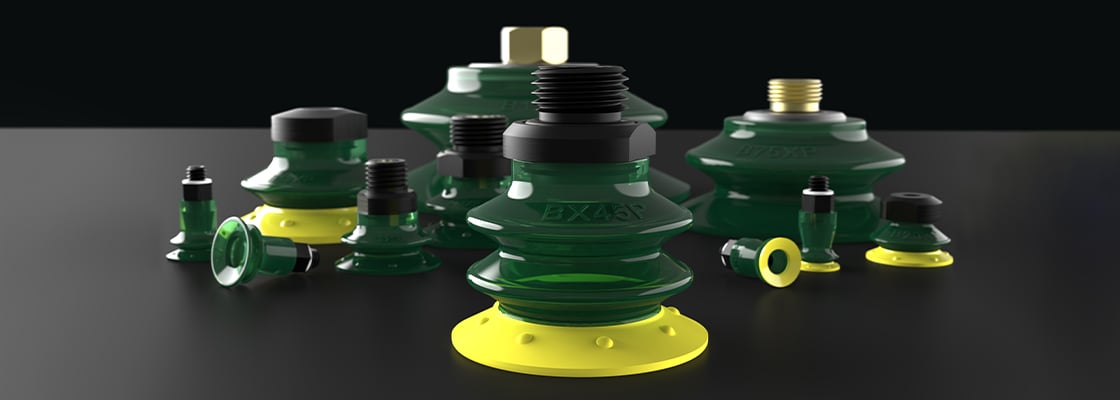
Product news
2025/5/13
Piab 推出 piCLASSIC™ Neo – 在现代化和可持续真空技术领域迈出了新的一步
Piab 推出引以为豪的 piCLASSIC Neo™,这是其广受好评的 piCLASSIC™ 真空发生器系列的最新产品。piCLASSIC Neo™ 系列旨在满足现代工业不断变化的需求,将效率、适应能力和可持续性相结合,为真空技术树立了新标杆。
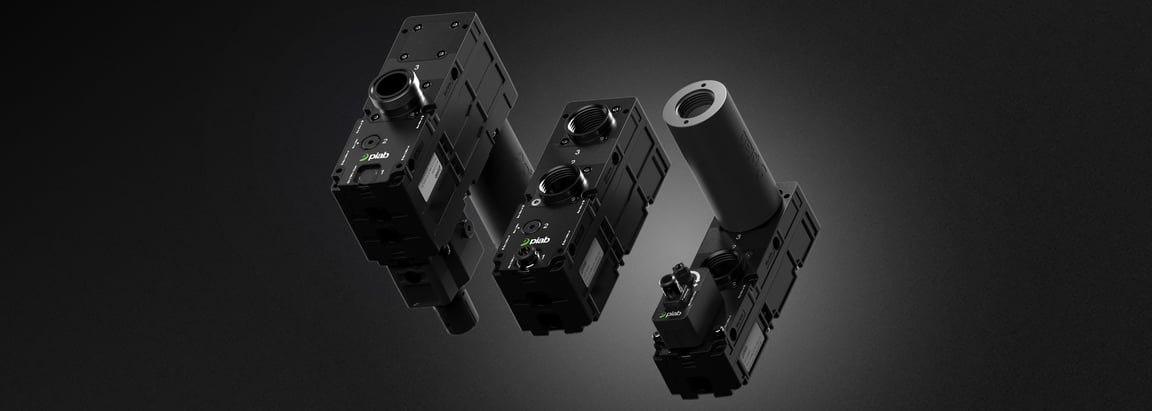
Product news
2025/4/29
推出 Polyscope X 兼容性:通过 Piab 解决方案增强 UR 机器人
Polyscope X 兼容性标志着 Universal Robots 能力的一次重大飞跃,使用户能够无缝过渡到更高效、更灵活的自动化解决方案。这项全新的兼容性确保了 Piab 的创新产品能够充分发挥 UR 机器人的增强功能和性能。
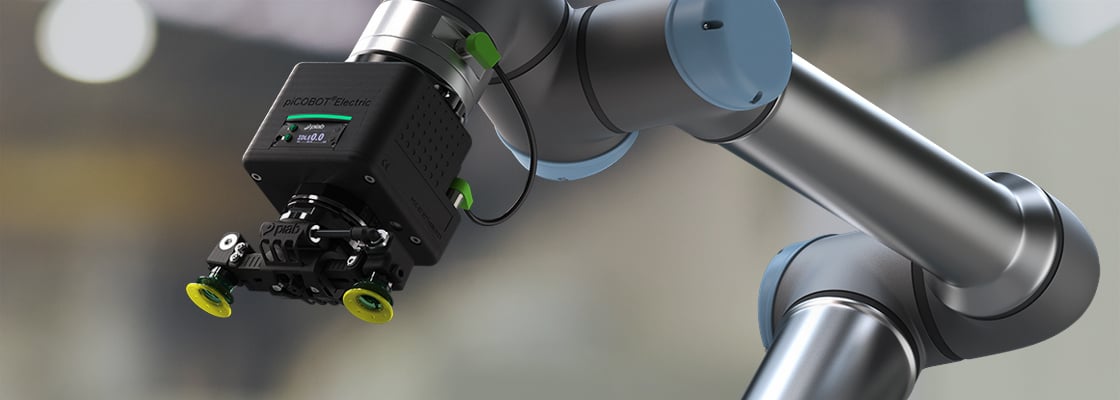
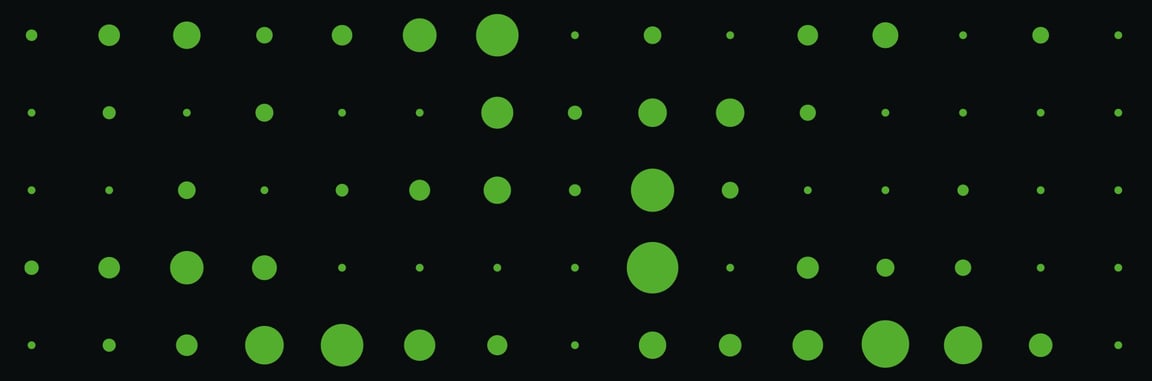
注册
创建您的免费账户以访问我们所有的内容
- CAD文件
- 可供产品
- 数据表
- 请求报价
- 手册
- 请求报价
- 白皮书