Automatic handling of cheese slice pouches of different formats at high process speeds
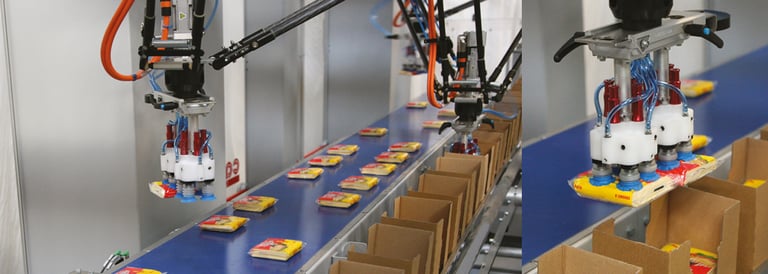
With the use of piGRIP® suction cups, certified for food contact, and COAX® vacuum generators, both Piab's products, CAMA Group has created a cutting-edge packaging system that allows to handle 280 pouches of cheese slices per minute.
In a complete line for the packaging of cheese slice pouches, precisely on the loading machine, CAMA Group has installed grippers made of plastic material using Piab’s piGRIP® FDA approved suction cups together with COAX® vacuum generators, Piab's highly efficient vacuum ejector.
The process is characterized by a very high number of pouch formats to be managed: ten product formats and about fifteen box formats, with many possible combinations. Leading up to more than 100 formats in total. In case of multiple formats (box plus pouches) weights of up to 1 kg [2.2 lb] can compile.
The first requirement was to minimize the replacement of the grippers resulting from format changes. CAMA Group has thereby developed two types of grippers, with which the company is able to handle all formats of cheese slices: one with 2 and one with 3 gripping units. Each unit consists of 4 suction cups and 4 vacuum generators and grips one pouch of cheese slices at a time.
Another critical parameter of the process is the high speed with the consequent risk of damaging the flow packs, resulting in the possible creation of undesired wrinkles on the product.
“We were looking for FDA-compliant suction cups - which not all suppliers are able to deliver - that would allow us to handle different formats, at high process speeds, without damaging the products" explains Massimo Monguzzi, CAMA’s R&D Manager, responsible for the project. “With Piab we went straight to the point. We carried out feasibility tests with the help of the Italian branch’s technicians and we developed a gripping solution that is characterized by a great flexibility. Since each suction cup is coupled with a single vacuum generator, we can choose to operate only some of the four suction cups of each gripper. All this results in important savings in the consumption of compressed air and electricity. Before choosing Piab’s vacuum generators, we also tested some types of vacuum blowers. This technology failed because vacuum blowers have a response time that is too long, difficult in regulating vacuum and finally can lead to damages to the products, with consequent high production waste. We therefore focused on Piab's COAX® technology, which allows the vacuum generator to be installed close to the gripping point, solving all our problems. With regards to the suction cups, we opted for the use of four suction cups and decided to deploy Piab's piGRIP®, with a diameter of 34 mm, at every location of the gripper. The reason is that this solution offers a solid grip, but leaves no marks on the pouches, and hence turned out to be the optimal solution for our process.”
The piGRIP® is a unique configurable suction cup concept with individually optimized parts for gripping, lifting and height compensation. Packaging small bags in cartons is the specialty of Piab’s piGRIP® suction cups that have specifically soft lips to hold on to the changing surface of a bag. They allow secure and quick moves to enable fast automated processes.
Piab’s vacuum generation technology COAX® minimizes energy consumption, while offering a secure and fast grip due to its high initial vacuum flow. COAX® ejectors are up to twice as fast as other ejectors and deliver three times more flow than a conventional vacuum ejector with identical air consumption. The pump unit can deliver high performance even with low or fluctuating supply pressure. This was proven in independent comparison tests at the Fraunhofer Institute for Machine Tools and Forming Technology IWU in Dresden. These tests have shown that the Piab ejectors require significantly lower compressed air to achieve the same output compared to ejectors from other manufacturers. Accordingly, their use reduces the cost of providing compressed air and thus the total cost of production.
Want to know more? Contact us!
About CAMA Group
Since 1981, CAMA is an international leading company whose core business is the engineering and the production of complete high technology secondary packaging systems for major multinational groups both in the food and non-food markets.