Safe powder handling for additive manufacturing
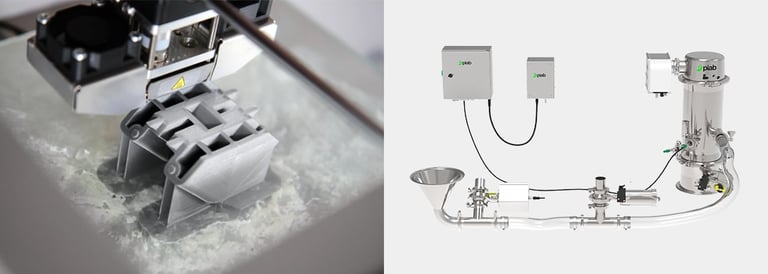
With Piab piFLOW®p SMART vacuum conveyors, the production powder can be easily delivered to the additive manufacturing (3D printing) systems without any particulate matter pollution for the employees. Thanks to the system’s intelligence and self-learning features no tedious setting and testing is required – just the press of the start button.
Everyone is today talking about additive manufacturing or 3D printing as one of the future technologies to meet the increasing demand for personalized or customized products. Originally used as a simpler solution in prototyping, more and more unique pieces are being produced using this technology. But while it sets standards in the realization of products, many process steps are still manual. This includes, in particular, the loading of the production equipment with the corresponding plastic or metal powder. An ergonomic workplace design is needed to prevent back pain from employees handling the weight of the containers as well as exposure to the particulate matter itself.
The use of vacuum conveying technology can help to protect people, the product itself and the environment. As a supplier to the pharmaceutical, chemical and food industries, Piab faces this issue daily and draws on 40 years of experience. Accordingly, the piFLOW®p SMART vacuum conveyor was developed as a closed system to solve this problem. Filters in the vacuum conveyor as well as additional exhaust air filters on the vacuum pump prevent fine dust from entering the system in the workspace and thus causing employees to come into contact with these substances. This ensures a clean working environment where the health burden is reduced as far as possible. At the same time, the powder is protected against contamination by environmental influences with corresponding loss of quality.
As it becomes ever important to ensure powders and granulates are conveyed in a controlled manner to dosing and mixing equipment, the autotuning feature of the new piFLOW®p SMART vacuum conveyor automizes the process of powder and bulk conveying. Based on its renowned COAX® ejector technology, the piFLOW®p SMART is pre-programmed with advanced algorithms to eliminate complex manual timer settings and allows continuous adaptive automatic fine tuning of the conveying process as well as recipe handling. Being able to independently adjust to different requirements enhances the conveying cycle tremendously. Equipped with advanced sensor technology, it optimizes and increases throughput up to 50% higher compared to conventional conveyor systems. Smart electrical control data collection and analysis for overall process optimization, and real-time adjustment become part of the daily routine.
In addition to its Industry 4.0 related features such as IO-Link, and the ability to preset, the new piFLOW®p SMART vacuum conveyor is equipped with further elements that allow easier and safer product handling. They are among others, automatic filter cleaning, multiple filter shock, material safety blockage function and antistatic filters and seals upon request. The system also recognizes and prevents overfilling or respectively that the container is emptied. That way the entire filling volume of the container can be utilized, which optimizes the material throughput.
The production time in the 3D printing process can be relatively long and the active conveying times are low. Thanks to the automatic shutdown of the vacuum pump at idle, the piFLOW®p SMART vacuum conveyor is very energy-efficient, especially in comparison to mechanical pumps, which must continue to run at idle. Thus, the energy costs for the automated delivery and filling remain low. Alternatively, it is also conceivable that the vacuum conveyor on a mobile platform feeds several 3D printers that use the same powder.
In addition to the conveying of new powder, the vacuum conveyors are also used to return excess powder from production back to the production cycle. In this case, the remaining powder is taken up by means of a suction feed using the vacuum pump of the conveyor and emptied through a sieve into a container. From there, the powder is fed back to the production cycle via the vacuum conveyor via a hose. In this way, the cycle is closed, resources are saved and waste is avoided. This reduces costs and protects the environment.
For Piab itself, additive manufacturing as a production technology is very interesting. Already today custom grippers for the handling of bags in the packaging of food are produced by this process. In particular, the lightweight construction potential is a great advantage for Cobot applications in addition to the individual design possibility.